A steel foundry is a manufacturing facility where metals—steel, iron, aluminum, and a few others—are heated until they turn into liquid. The liquid metal is then poured into a specifically-articulated mold. When that molten metal solidifies and is removed from the mold, the result is a product or component that might be used in any number of products, including many that have become essential to modern life.
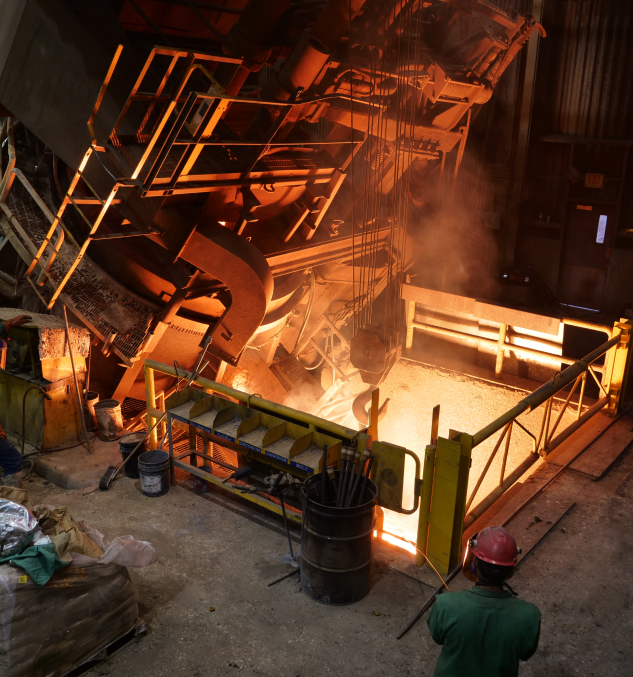
How Does a Steel Foundry Work?
Every foundry has the necessary equipment, protective gear, and other devices necessary to keep workers safely operating this equipment. The heat required to melt metal is, as you might expect, quite intense. To reach such a high temperature, foundries use furnaces in the earliest stages of the metallurgical process. While there are different types of melting furnaces, the goal is always to use the least amount of heat required to turn the solid metal into liquid metal.
What Can a Steel Foundry Produce?
A foundry produces metal castings. The most common metals used in this process are aluminum and cast iron. This means that steel foundries produce an almost endless list of products and components—everything from the pipes carrying your city’s water supply to the large beams used in heavy construction. At Harrison Steel, our in-house machining capabilities allow us to produce perfect, finished parts (not just rough castings) faster and more cost-effectively than outsourcing, as many other foundries rely on.
What Is the HSC Steel Foundry Process?
We work diligently with our customers up front to create a fair and accurate quote range for each project. Nobody likes price creep or surprises.
We use the most advanced three-dimensional engineering software available and hyper-detailed simulations that allow us to anticipate issues long before a part is ever cast. Mold designs and production processes are perfected from the start.
We bring a seasoned, skillful eye to the process in our full-scale commercial pattern shop, where—as always—our goal is a highly efficient, zero defect product. We rigorously study the chemical and physical behavior of the metal alloys we use. Then we take all that scientific expertise and translate it into a consistently strong, durable final part for our clients.
We’re one of the only steel foundries in the country that uses this shroud pouring, a tech-forward process that minimizes air entrainment and potential defects. The result is a cleaner and far-stronger casting.
Every part is inspected at the deepest, below-the-surface level to ensure consistency using our comprehensive nondestructive testing: wet/dry magnetic particle inspection, UT, gamma ray, and electro optical dimension verification.
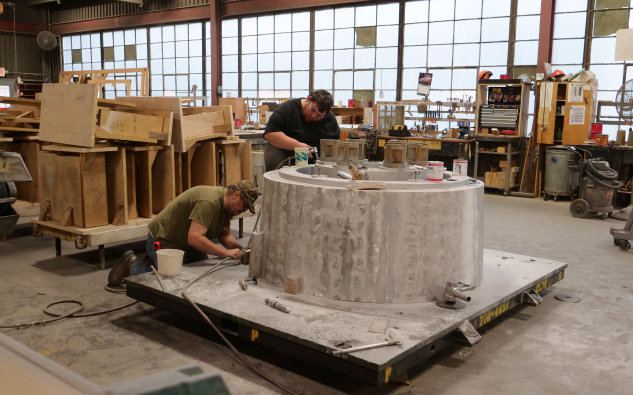
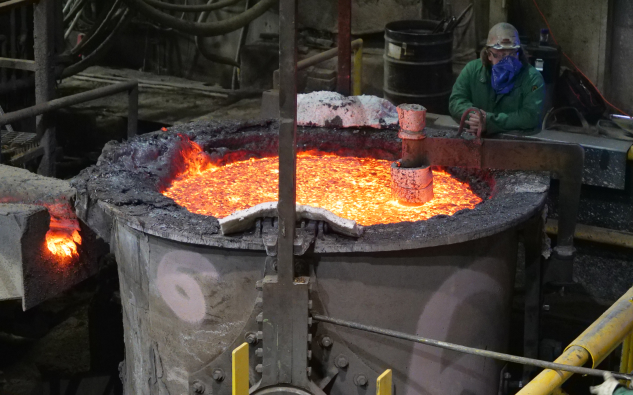
What Is It Like Working in a Steel Foundry?
Our jobs are reserved for people who take pride in what they do and aren’t afraid of a challenge. The casting process requires an army of diverse skills to move from concept to completion, from the deepest thinkers to the toughest workers. In short, we want people who see Harrison Steel the way we do: a hardworking, dedicated family producing a high-quality product. Sound like you? We offer our employees competitive wages, ongoing training, excellent benefits, and a place to sharpen and develop lifelong skills